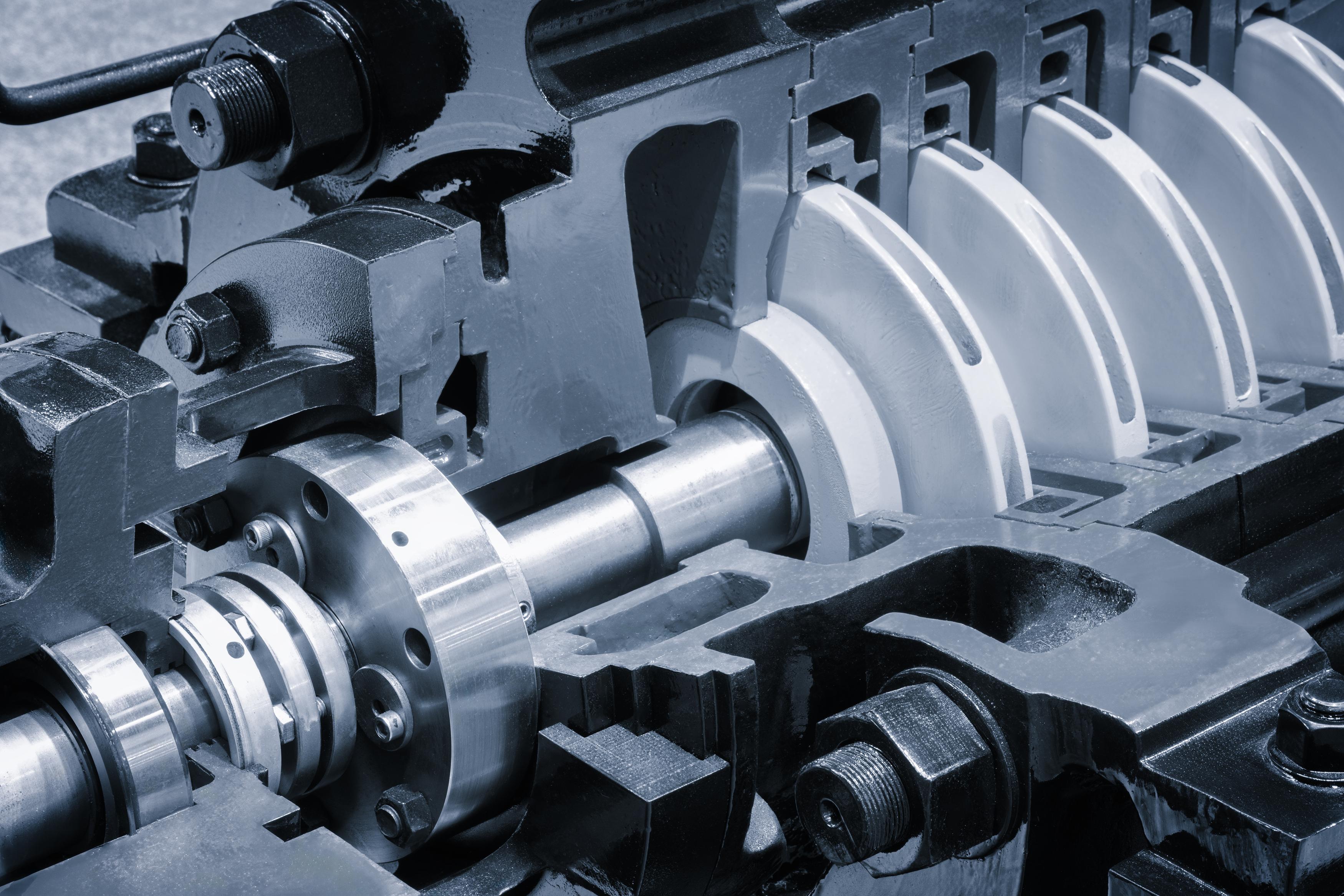
7 Common Failures of Multistage Centrifugal Pumps
- Katarina Knafelj Jakovac
November 27, 2023
The most common rotational machines in industrial and manufacturing facilities are single-stage and multistage centrifugal pumps.
A centrifugal pump is a machine in which the mechanical energy of the driving machine, usually an electric motor, is converted into the kinetic energy of the pumped fluid.
The diagnosis of centrifugal pump failures has extensively evolved from the time before 50 years ago when the sound of a faulty bearing was among the few indicators for an experienced mechanic to understand what troubles a malfunctioning pump and why it happens.
Multistage centrifugal pumps are structurally designed with multiple rotors of smaller diameters mounted one after another on the same shaft and less clearance between the wear rings of the rotor and the casing according to the API 610 and ISO 13709 standards.
The pump overheats during operation.
In image, a schematic of a pump with 12 rotors, i.e., 12 stages and its components are shown. All rotors are housed in a common casing.
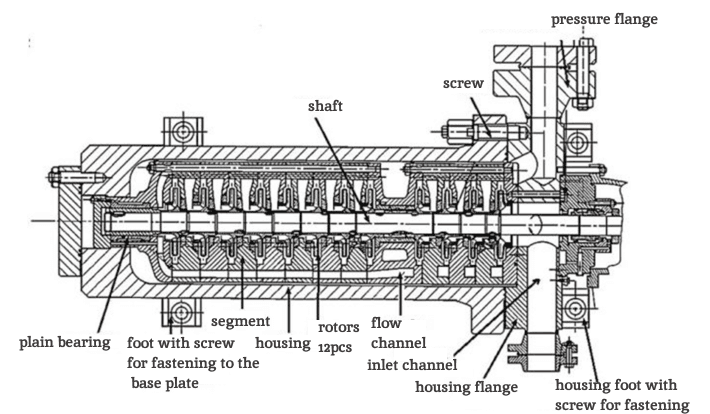
Image: Cross-section of a multistage pump and main components
The shaft rotates all rotors in the same direction, so they behave in operation as multiple separate single-stage centrifugal pumps mounted in a common casing.
When the fluid flows from one stage or rotor to another, the delivery head proportionally increases, resulting in higher pressure achieved by the multistage centrifugal pump compared to a single-stage centrifugal pump.
An additional advantage is that multistage pumps achieve better efficiency with a lower-powered electric motor and the use of less energy.
On the other hand, single-stage centrifugal pumps achieve higher flows and lower pressures and are suitable for installation in process conditions where there is a need for large flows of working media.
The lack of small clearances between the rotor and the casing prevents the pumping of working media containing abrasive particles, impurities, or solid pieces.
Therefore, multistage centrifugal pumps are used for clean working media such as water and low-viscosity liquids like gasoline, fruit juice, and alcohol.
The pump casing can be cast in the form of a single cylinder, so we say it is a barrel pump, or it can be assembled from a series of segments, with each rotor within a separate segment of the casing.
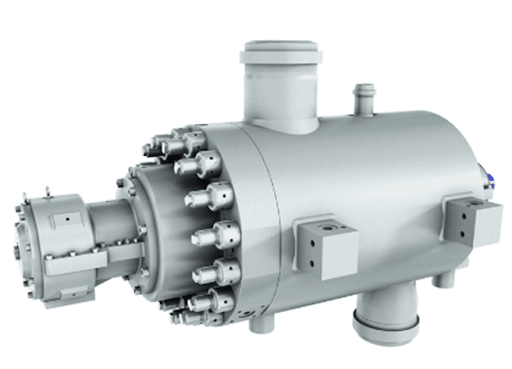
The axial load on the shaft is on sliding bearings, while radial loads are carried by ball bearings most commonly. Each multistage pump has 2 mechanical seals located to and opposite the coupling.
The casing is made in one piece and horizontally divided into two parts.
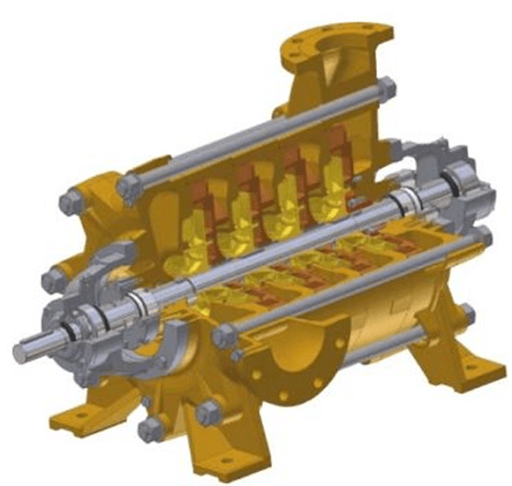
Failures are most often the result of inappropriate operating conditions, insufficient maintenance, inadequate design, assembly errors, or a combination of the above.
The most common symptoms of failures that occur in multistage pumps are:
1) The pump does not supply on the pressure side after startup.
The cause is insufficient amount of working media in the casing (we say that the pump must be fully submerged) or there are residual air pockets in the casing and suction pipe.
Other causes are insufficient rotation speed, incorrect rotation direction, a clogged rotor, or a clogged suction at the casing inlet, as shown in the picture.
To eliminate these causes, it is necessary to ensure that the pump casing is completely filled with working media at the appropriate temperature and vented, with the suction valve 100% open.
Check if the motor phases are properly connected and verify whether the electric motor achieves the required rotational speed. On one occasion, motor phases were swapped, and the electric motor rotated the multistage pump in the wrong direction. The consequences were quickly evident in the form of damaged internal and external seals and minor damage to the front bearing.
2) The pump does not achieve sufficient flow or the required delivery head.
Again, the cause can be the wrong direction of motor rotation, blockage of the pressure pipe, clogging of the suction filter, and too low rotational speed.
Additionally, air pockets in the casing, damaged wear rings of the casing or rotor, and a damaged rotor, as shown in the picture, also prevent achieving sufficient flow or delivery head of the working media.
The suction filter or strainer should be regularly cleaned, ensuring that the suction and pressure pipes are clear. Often, Y-type suction strainers are mounted on the suction pipes of pumps.
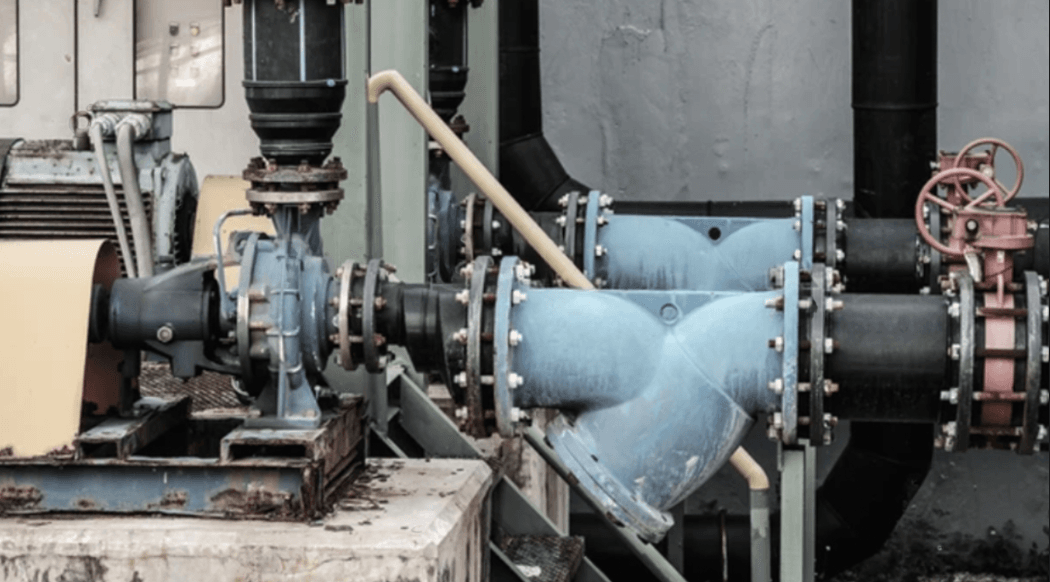
Picture: Y-strainer on the suction pipeline of the pump
Y-strainer or filter is named after its shape and the fact that it can be easily mounted in a horizontal or vertical position, depending on the configuration of the pipeline.
The pump must be vented before starting and inspect the condition of the rotor and wear rings during each service (are there any cracks, surface damage, presence of corrosion, erosion, etc.).
During the assembly of the rotor assembly, ensure the proper clearances between the rotor and the casing, the balance bushing relative to the stator, the sliding bearing relative to the sleeve, and the rotor hub relative to the diffuser.
The table shows an example of the required clearances from the user manual of the original manufacturer in inches and millimeters:
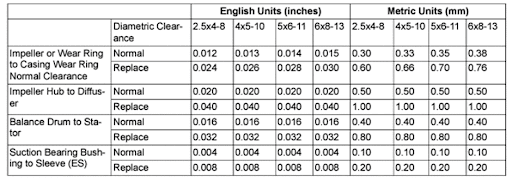
3) The pump shuts down soon after startup and consumes higher or lower power than required during operation.
The cause of these failures can be too low or too high rotational speed, a faulty electric motor, and too high or too low viscosity of the working media.
This type of failure can also be caused by incorrectly installed front and rear seals, misalignment of the pump unit, and overly tight tightening of one or both seals.
Ensure that the working medium has the required viscosity, regularly check the electric motor, and lubricate as needed.
During the assembly of the pump, pay attention to the correct installation of the bearings and ensure the appropriate tightness of seals.
Before starting the pump, check if the pump and electric motor are aligned and correct as needed.
4) The seal is leaking working media.
Leakage usually occurs due to damage to the sealing faces on the rotating and stationary rings due to friction of excessive particle quantities in the working medium over the sealing faces.
Excessive axial force on the rotor assembly puts a strain on the sealing element, causing it to fail, and it could also be that the wrong type of sealing element has been chosen.
Always install a filter or mesh strainer in the suction pipeline, ensure that the pumping pressure is maintained properly (chemical and physical properties of the working medium must be within allowable limits defined for each pump), and check with the seal manufacturer if the correct type of seal is selected considering the operating conditions.
5) The pump has increased vibrations or operates very noisily.
Large air accumulations within the casing can cause this behavior during operation, or when the suction valve is not fully open.
Then, when the NPSH is too low or the pump does not reach the working point, the rotor assembly is unbalanced, the wear rings are damaged, or the bearings have worn out.
The sound of a faulty bearing is irregular and intensified, resembling the sound of rolling stones, scratching, squeaking, or squealing, which increases as the rotational speed of the shaft increases.
In everyday life, such sounds are most commonly heard when there is damage to a bearing on a car wheel.
Eliminating the causes of increased vibrations and noisy pump operation starts with the simplest check: whether the suction valve is fully open and the pump is completely vented.
Check in the user manual what the required NPSH and working point of the pump are and whether the pump meets the specified conditions in the current state.
Vibration measurements will determine whether it is necessary to balance the rotor assembly or if there is damage to the wear rings, intermediate bushings, and bearings.
Intermediate bushings are parts of the pump designed to maintain balance during axial shocks created by rotors.
The bushings maintain stability by reducing the force acting on other parts of the pump and prolonging the life of the thrust bearing by influencing friction reduction.
A damaged intermediate bushing will severely disrupt the dynamics of the rotor assembly, and it must be replaced during the assembly of the pump.
During each service, it is necessary to balance the rotor assembly on a balancing device and in accordance with the requirements of the ISO 21940 standard, as shown in the picture.
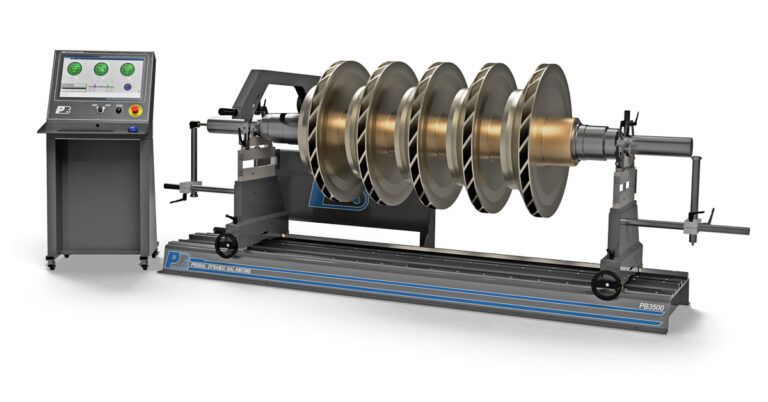
Image: Dynamic balancing of the rotor assembly of a multistage pump (Source)
6) The bearings overheat or wear out too quickly.
The misalignment of the pump unit, incorrect lubricant and insufficient lubrication of the bearings, and a damaged coupling are largely the cause of this failure.
Then follows the imbalance of the rotor assembly and too high axial force during operation.
Regularly lubricate the bearings and use only the types of lubricants recommended by the pump manufacturer, as shown in the table where lubricant manufacturers are listed in the first column and types of oils for lubrication are listed in the second column.
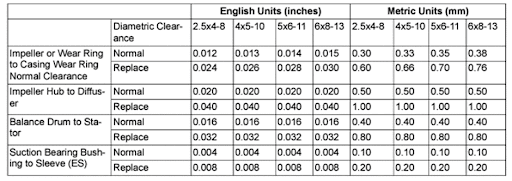
Check whether the lubricant has the appropriate viscosity.
When installing new bearings, install only types of bearings specified by the pump manufacturer in the technical documentation.
The installation of bearings of unknown origin, from an unknown manufacturer, or bearings for which it is not known how long they have been in storage is strongly discouraged as it will lead to the recurrence of the failure or even worse consequences.
Measure vibrations at regular intervals and record the results that will indicate whether there is an imbalance and how much time is left before the bearings fail.
If necessary, laser align the pump unit again, as shown in the picture.
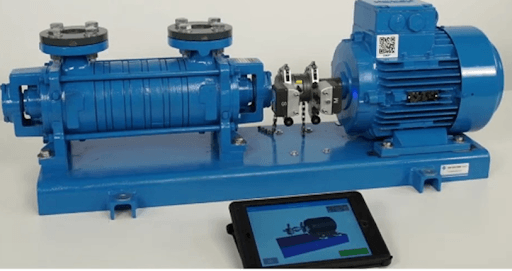
7) The pump overheats during operation.
The cause of this failure is friction among the pump parts that have loosened, causing friction, shaft misalignment, overly tight tightening of the seals, and excessive axial force on the rotor assembly.
During each service, assemble the machine parts correctly and check the condition of the shaft on a lathe (we say that the shaft "throws" on a lathe beyond the allowed limits) or on a balancing machine.
Before installing the coupling, check whether the seals are properly tightened, align the unit, and after starting, ensure that the pump has achieved working conditions: pressure, temperature, and flow.
Diagnosing failures in multistage pumps is more complex compared to a single-stage pump because it needs to cover more potential causes and their interactions.
Often, in practice, several factors simultaneously cause a certain failure, so it is necessary to investigate in more detail what is happening.
When some failures recur, and preventive measures do not work, it is recommended to contact the pump manufacturer for additional technical advice. If the pump is under warranty, factory service or replacement can be requested.
Regularly conducting preventive maintenance using reliability-focused maintenance techniques will ensure uninterrupted operation of multistage centrifugal pumps, extend their service life, and increase machine reliability.